The Differences and Benefits Between CNC Machine Monitoring and Production Machine Monitoring
Maximizing efficiency and minimizing machine downtime are key priorities for those in charge of production in today’s smart factory and data driven manufacturing landscape. Achieving these goals is getting tougher to realize with supply chain issues, increases in raw material prices and industry expertise leaving and not being replaceable with ease the way it was in previous generations. To combat these omnipresent issues, manufacturers have been turning to smart factory machine monitoring systems. However, the choices of machine monitoring systems have become vastly saturated within the last decade. There are more brand options, different feature sets, widely varying pricing structures, and different scopes of applicable use. The sole tie that binds is the moniker “machine monitoring” somewhere in the product description. A quick Google search for “machine monitoring” will retrieve pages and pages of results that might not actually be what you are looking for. In the following thought piece from Scytec, we will be identifying and describing the provisions of two of the most common “machine monitoring” platforms, CNC machine monitoring and production machine monitoring. While CNC (Computer Numerical Control) machine monitoring and production machine monitoring may seem similar from a distance, they serve distinct purposes and are tailored to specific aspects of the manufacturing process.
What is CNC and Production Machine Monitoring?
First off, let us discuss the high-level differences between the two. CNC machine monitoring focuses specifically on CNC machines, which are precision tools used for machining parts with high accuracy. I would also like to stress that CNC machine monitoring is not just limited to CNC machines. Robust machine monitoring platforms like Scytec DataXchange can retrieve useful data points from all shop floor production equipment like fabrication presses, brakes in addition to custom machines such as assembly lines. A host of machine sensor types including humidity, fill level, proximity, and thermocouples can also be monitored with Scytec DataXchange. These machines are commonly found in industries such as aerospace, automotive, and medical device manufacturing. Monitoring CNC machines involves tracking various parameters and metrics unique to their operation, including OEE, the real time/current and historical status of the machine as well as part tracking, spindle performance, high and low override tracking, alarms, downtime reasons and many more. Compared to production monitoring, CNC machine monitoring platforms like Scytec DataXchange can give users a richer set of data that comes direct off individual machinery and details necessary parameters that production machine monitoring might not such as mode from the controller on the machine and the axis feed rate of a controlled axis.
Production machine monitoring, on the other hand, takes a broader approach than CNC machine monitoring, which is more focused. It focuses on the entire production process and involves monitoring various types of machines and systems used in manufacturing. Production machine monitoring gathers data from multiple sources outside of machinery doing the actual product production and considers overall plant performance and typically does not get to the level of detail that CNC machine monitoring achieves. A commonly used tool for production monitoring would be a data listener, like a bar code scanner, that would scan the items coming off a conveyor belt for distribution. Key aspects of production machine monitoring that are examined include OEE, process flow between different stages of production, energy consumption, and maintenance needs.
Do some of these trackable tenets cross over to both mentioned machine monitoring platforms? Absolutely, OEE and other tenets can be tracked between the two and there are CNC machine monitoring platforms that give end users the bare minimal in terms of reported metrics. That might be all what a certain shop floor requires as well. Your choice between CNC machine monitoring and production machine monitoring comes down to the needs and output of your operation regarding scope, purpose and your integration needs as well as the amount of detail you need collected from your machinery. Vetted industry standouts like Scytec DataXchange give end users a litany of useful information that can be pulled off machines in several different ways allowing users to access information crucial to their shop floor and making sure that all shop floor equipment can be tracked with DataXchange’s stout assortment of connection methods.
Both CNC machine monitoring and production machine monitoring play vital roles in today’s manufacturing environments. CNC machine monitoring ensures precision and reliability in critical machining operations, while production monitoring delivers the big-picture insights needed to manage the entire manufacturing process.
Which Machine Monitoring Platform is Right for You?
After discussing what are the differences between CNC machine monitoring and production machine monitoring, you might be asking yourself which is the right one for your production environment. Both types of machine monitoring platforms may be appropriate for your environment and deciding on which one to purchase might come down to a balancing act of which one fits the bill in terms of budget, features offered, how they can alleviate concerning production needs and issues you are faced with on the shop floor.
To ensure that your individual equipment is playing its well-tuned part, acting like an individual instrument in the orchestra that is your shop floor, Scytec DataXchange machine monitoring was developed in mind for all manufacturing needs and scenarios. DataXchange offers low month-to-month pricing and no minimum on machines, so manufacturers can receive only the metrics they need and are not beholden to unfair contracts made for factories not indicative of their own. DataXchange can also integrate with ERP systems like JobBoss and digital twin standard Vericut. Scytec DataXchange also services a wide range of output types by applying utility to low mix, high volume shop floors as well as low volume, high mix production facilities. The utilitarian aspect of a robust machine monitoring platform like Scytec DataXchange cannot be ignored and has a place in any environment that produces anything.
To experience what the cutting edge of smart factory solutions looks like, click the link below for a personalized demonstration of what Scytec DataXchange machine monitoring can offer your shop floor.
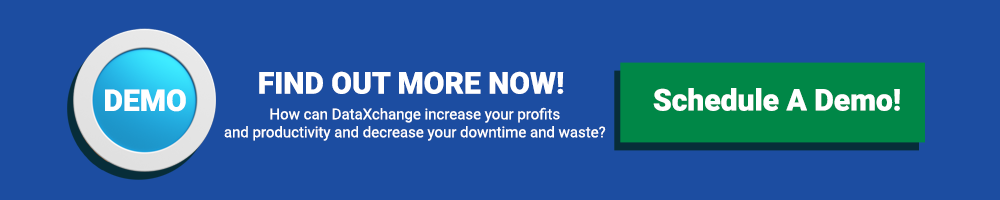