Do You Know the Secrets of What Your CNC Controller is Hiding?
Are you aware of the hidden treasure trove of information that is on your CNC controller? A litany of useful data that can be used to increase OEE, minimize downtime and a host of other shop floor improvements are waiting to be discovered. Scytec DataXchange, a machine monitoring platform that goes above and beyond rudimentary machine monitoring reporting, can deliver much needed metrics and observances that other machine monitoring platforms cannot. DataXchange achieves this by pulling a rich set of data off your CNC controller and then uses that information to produce compelling results in the form of manufacturing charts and dashboards to help manufacturers improve processes and confront bottlenecks. In this thought piece from Scytec we will be examining how DataXchange machine monitoring accesses and utilizes data points from your CNC controller that can be used to evolve your shop floor.
What is a CNC Controller?
CNC machines are equipped with controllers, and they act like the brain of the machine. This computer-based system oversees and directs the machine’s movements throughout the manufacturing process. It interprets instructions, executes programmed cutting or machining tasks, and ensures the machine operates as designed. This is done through G-Code input, and the controller interprets the G-code and translates it into electrical signals that control the machine’s motors and other components, guiding the tools to perform the desired actions. The CNC controller is the essential component that connects the digital design to the physical production of the intended part. DataXchange pulls information off these controllers via a machine protocol like MTConnect, OPC UA or Fanuc FOCAS.
How Does Machine Monitoring Work?
If you are already familiar with how machine monitoring works you can skip this section, but for those of you who are new to the prospect of the benefits provided by smart factory technology, this is a brief rundown of how machine monitoring works. A machine monitoring platform like Scytec DataXchange can pull information off a CNC controller via the aforementioned protocols, giving insight to those who demand it in regard to how a machine or group of machines is performing on their shop floor. This useful information is collected from machine controllers via DataXchange’s ability to read and interpret direct or open-source standardized protocols like MTConnect. Examples of direct protocols for common machine brands include Fanuc FOCAS and Okuma THINC. This amassed information is not limited to whether a machine is running or not running, nor is machine monitoring limited to just automatically pulling information off a CNC controller. Robust platforms like Scytec DataXchange can pull information off sensors from machines as well as receive operator feedback for information that cannot be automatically collected off a machine, such as if an operator went on a lunch break. These collected data items can be used to populate manufacturing charts and dashboards that can be viewed on smartphones, tablets, TVs and computers and promise to ease shop floor woes by increasing machine and workforce performance.
The DataXchange Difference
What separates Scytec DataXchange from other machine monitoring platforms is the ability for DataXchange to directly access protocols from well-known CNC brands like Fanuc, Okuma, Siemens, Heidenhain, Haas NGC and Mazak. Why does this matter? DataXchange’s ability to access these protocols allows for manufacturers to see that treasure trove of information hidden on your CNC control. This obtained information can be used to track all sorts of useful data items such as the tool position of active tools, alarm codes and their descriptions, whether coolant is active, whether a dry run setting is on or off, whether a machine is in an e-stop, whether a machine is in a M0 pause and much more. These useful collected data items do not stop at use with Scytec DataXchange machine monitoring either, but can also be applied to CNC Machine Connect, the integration between Scytec DataXchange and Vericut.
How Direct Protocol Access is Preferable to Standard Protocols
Earlier we discussed a few of the open source and standardized protocols like MTConnect. While they may be widely used in modern manufacturing, that doesn’t mean there are not any drawbacks. Standardized protocols may only be giving you only a portion of what you could be looking for, as they do not have the ability to read certain data points off a machine controller the way that direct protocol access supplies a richer set of data for end users. Support is something else to consider with the lack of direct protocol access, standardized protocols are not supported by machine tool builders or other third parties. Bugs are harder to fix and enhancements are harder to make across multiple different vendors. However, with the direct protocol difference from DataXchange you can reach out to the professionals at Scytec and evolve your shop floor with the hidden secrets of your CNC controller.
See For Yourself
If you would like to see what data points can be collected from your machines, then head over to the Scytec “Tech Supported” page and click on the brand logo of which of your machines you would like to see data points for. The list of supported machines that DataXchange can connect to is ever evolving as well, and we at Scytec encourage you to participate in a personal demonstration of how DataXchange can be deployed on your shop floor. Please head over to our schedule a demo page linked below and a Scytec team member will guide you through how you can improve your shop floor performance with DataXchange. You can also view our webinar about machine protocols below as well.
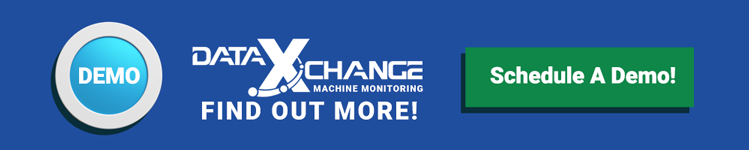