The Benefits and Challenges of Lights Out Manufacturing
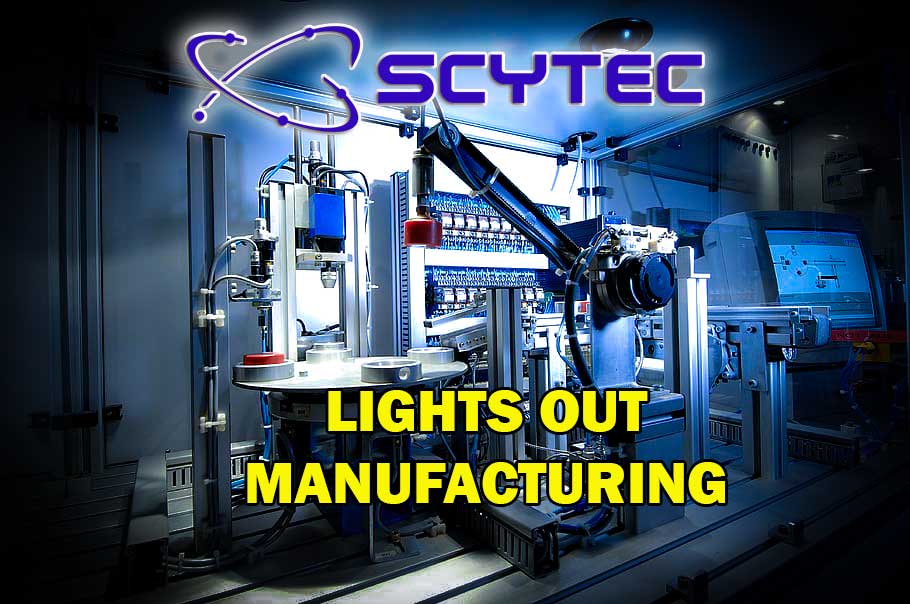
What Is Lights Out Manufacturing?
Have you ever heard the old industry joke that the factories of the future will be automated to the point that they will only have two employees? A dog to guard the factory and a human to feed it. So, what is Lights Out Manufacturing exactly? Quite simply, Lights Out Manufacturing is creating automation processes that are so minute and precise to the point where factory shop floors can literally leave their lights out. FANUC, a well-known Japanese manufacturing giant has successfully been operating with “lights out” since 2001. The facility that FANUC builds its automated machines and robots can operate in a lights-out operational setting for up to 25 days. Employees are hardly ever there for issues other than planned routine maintenance or for on-site emergencies. Humans are not at the factory to assemble products or move parts around the plant. Since the 1980s manufacturers have been focusing on adopting lights-out approaches during night shift operations that are traditionally harder for humans to adapt to. Because let’s face it, machines don’t need to eat, sleep or have outside work obligations.
The Benefits of a Lights Out Production Floor
Full automation can be of exceptional benefit, especially in hazardous manufacturing surroundings such as those with caustic chemicals, fumes, and other harmful materials to humans. Robots and other automated machines are made of more durable components than their human counterparts and artificial intelligence has yet to try and unionize. The obvious foundation of Lights Out Manufacturing is reducing costs and driving greater overall equipment efficiency (OEE), but also includes:
-Reducing accidents and increasing workplace safety
-Reduce scrap and achieve the best production consistency
-Drive more advanced maintenance strategies
The Challenges of Lights Out Manufacturing
In the ironic year of 1984, Apple promised the world they would attempt to be a lights-out factory at their 20-million-dollar Fremont, California plant at only a 2 percent increase in their products MSRP. Apple closed the factory down in 1992 because there were a few issues that needed to be ironed out before their CNC machines could go fully automated. The benefits that were listed above, would be enough for any manufacturer to jump for joy and begin immediate implementation for their entire manufacturing process. But there are plenty of hurdles that manufacturers need to focus on as well. Below we will outline what challenges that a producer will face when implementing lights-out manufacturing.
Technological Challenges
It is not as easy as just turning a switch on and off and expecting perfect results the first time and every time. Setting up completely automated processes can be a highly technical challenge that may require a hefty financial investment. Solutions like Scytec’s DataXchange enables manufacturers to easily and quickly collect data and use that machine data to determine how effective a machine or machine shop is operating.
Complex Production
Simple, repeatable tasks are the best fit for automation equipment. More complex tasks, as well as small-scale production runs and operations, may prove more difficult to roll out automation or experience enough value.
Prevention and Safety Techniques.
The big catch with having zero humans around a shop floor is what happens when something goes haywire? Let’s face it at some point something will go wrong in a production environment and it could require some kind of human intervention. This could result in tremendous financial damage to raw materials, physical real estate, machines, and equipment. Luckily, remote monitoring and automated machine failure detection can work to avoid these issues and there are companies like FireTrace that offer fire suppression systems for machines.
Scheduled preventive maintenance is a necessity for lights-out factories. Sensors can pick up on problems with machinery and react in time before a disaster occurs. A single-person approach, where one operator monitors all processes from a remote location and can take effective remedial action in case of emergencies or mishaps, is also common. Companies like Scytec offer products like DataXchange remote monitoring features, which enable users to monitor automated processes with a smartphone or other device. Click here to schedule a demo of this revolutionary platform to help your shop floor go lights out.