The Difference Between Utilization and Cycle Time
In DataXchange two commonly used reports and charts are the Equipment Status Summary and the Target Utilization. The Equipment Status Summary shows the statuses that have occurred over the period of time selected, while the Target Utilization shows the utilization percent relative to a target.
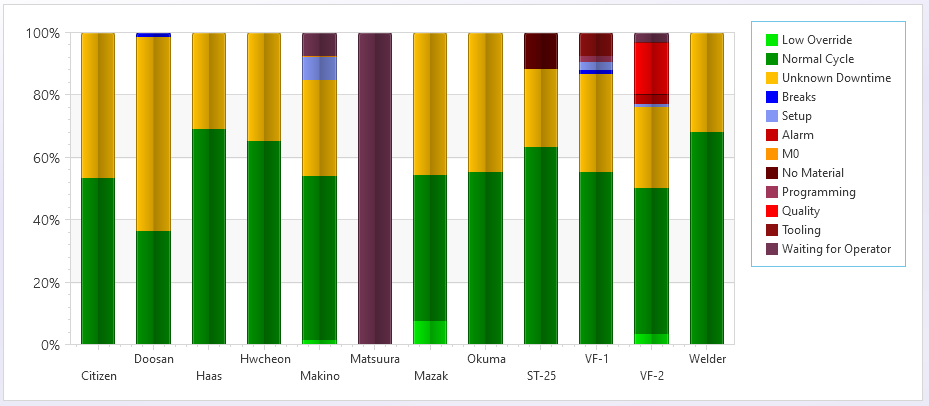
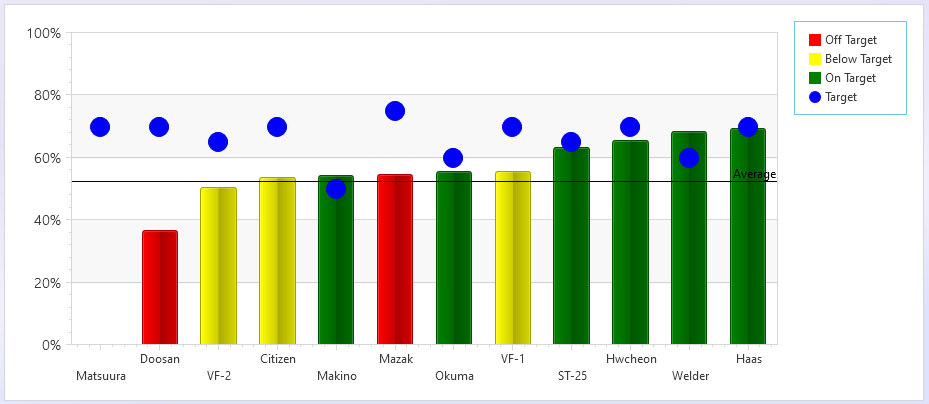
A common question is whether or not the percent of cycle time in the Equipment Status Summary should match the utilization percent in the Target Utilization. The answer to the question is, maybe…
There are a few things to consider here when answering this question.
What is the definition of utilization? For example, if Warm-up is tracked as a cycle status should the warmup time be counted as part of utilization? The machine is running, but not producing.
Should utilization be calculated over the entire time frame in consideration? For example, if the machine is only scheduled to run 20 hours out of a 24-hour day should the utilization calculation be based on 20 hours or 24 hours?
You know how it goes, ask two people, get three answers, and none of the answers are necessarily incorrect. Scenarios such as this are why the options are configurable in DataXchange.
The utilization calculation is Actual Run Time divided by Total Time. Both the actual run time and the total time have configuration options.
Selecting the General In Cycle option will include all cycle statuses as run time. However, selecting individual specific cycle statuses allows for any cycle status to be excluded from the amount of run time used in the calculation.
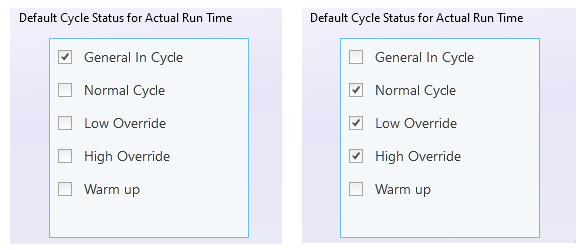
When it comes to the total time aspect of the calculation there are a few options as well. If shifts are being used then the shift times can automatically be used as the total time. Note that this could result in a utilization number greater than 100%, and this isn’t necessarily a bad thing. A scenario such as this could happen if overtime run scheduled. Seeing the utilization was 110% of the shift time can tell you valuable information.
Another option relating to total time is the ability to subtract out Planned Downtime. For example, if there was planned maintenance for 2 hours should that time count against the utilization number?
When using these options it is important to consider the expressions that have been assigned to the machines. If there is an expression that automatically places the machines in a planned downtime when a shift is not active then you do not want to set both the Use defined Shift as Total Time and Subtract Planned Downtime From Total Time to True as this would result in the non-shift time being subtracted twice.
The Subtract Unplanned Downtime From Total Time and Subtract Unknown Downtime from Total Time are options simply for ‘completeness’, but we don’t recommend using them in most scenarios.
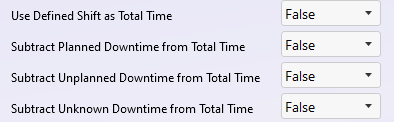
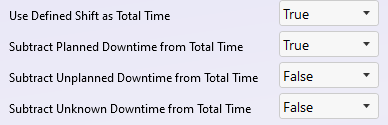
The ability to calculate utilization separately from cycle time and see both is a powerful tool in Scytec DataXchange allowing you to understand how well you are doing relative to how well you should be, while still showing that there may be opportunity to improve.